Cryogenic tank insulation
Insulation for cryogenic tanks is essential for maintaining ultra-low temperatures for storing cryogenic liquids, such as liquid oxygen, liquid nitrogen, hydrogen, and LNG. Even small heat transfers can lead to significant evaporation loss when these liquids are stored below -150degC.Cryogenic tank insulation reduces heat transfer, ensuring integrity and efficiency. Cryogenic tanks can utilise a variety of insulation types to minimise heat transfer and sustain extremely low temperatures for the storage of cryogenic liquids. The insulation types in Cryo tank are broadly classified into three categories: vacuum, foam, and powder/granular insulation. Each type has its specific applications, advantages, and limitations. Here’s a detailed breakdown:
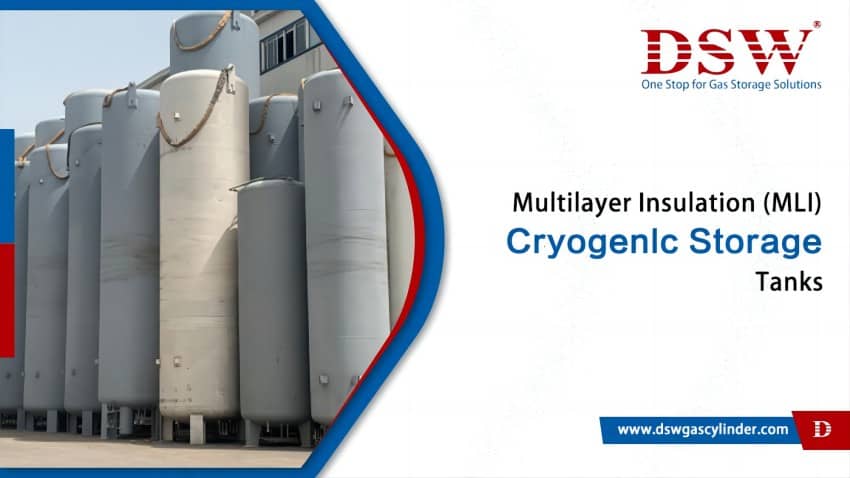
1. Vacuum Insulation
a. Vacuum Jacketed Insulation
- Vacuum insulation (vacuum jacketed or double-walled insulation) creates an internal vacuum between two tank walls to draw out air and drastically decrease heat transfer by convection and conduction.
Cryogenic tanks with vacuum insulation typically have an inner vessel that stores cryogenic liquid and an outer vessel. Any space between these vessels must be evacuated to create a high vacuum. - Advantages: Provides superior thermal insulation and is especially adept at lowering boil-off rates, making this solution suitable for long-term storage or transportation.
- Applications: High-performance cryogenic storage tanks are frequently used for industrial gases, space applications and LNG storage.
b. Multilayer Insulation (MLI)
- Vacuum-insulated tanks are often combined with MLI, which involves alternating layers of reflective material (like aluminized polyester or Mylar) and low-conductive spacers. These layers reduce radiative heat transfer within the vacuum space.
- Advantages: Reduces radiant heat transfer; highly effective in combination with vacuum insulation.
- Applications: Used in space applications, high-performance cryogenic tanks, and in combination with vacuum jackets.
c.Perlite-Filled Vacuum Insulation
- This type of insulation combines vacuum technology with loose-fill materials like perlite in the space between the inner and outer vessel walls. It maximises infrared radiation absorption and reduces convective heat transfer within the vacuum.
Structure: Perlite offers structural support to the vacuum jacket, creating a partial vacuum in a perlite-filled space, which is then evacuated to form a low-pressure environment. - Applications: It is suitable for cryogenic storage vessels where maintaining a vacuum, such as LNG or industrial cryogenic gas storage tanks, may be brutal.
- Advantages: provides a cost-effective solution with good thermal insulation properties, offering advantages over MLI and high-vacuum systems, including reduced costs and effective thermal management.
2. Foam Insulation
a. Polyurethane Foam
- Description: A closed-cell foam sprayed or applied as panels to the tank surface.
- Advantages: Good insulating properties, relatively easy application, and cost-effective.
- Applications: Widely used in both storage and transport tanks.
b. Polystyrene Foam
- Description: A type of plastic foam used in cryogenic insulation, though less common than polyurethane.
- Advantages: Low thermal conductivity, lightweight.
- Applications: Sometimes used in storage applications.
3. Powder/Granular Insulation
a. Perlite
- Description: An expanded volcanic glass that forms a lightweight insulating material.
- Advantages: Low thermal conductivity, cost-effectiveness, and good cryogenic performance.
- Applications: Often used in larger storage tanks and some transport tanks.
b. Aerogel
- Description: A highly porous, low-density material known for excellent insulating properties.
- Advantages: Extremely low thermal conductivity, lightweight, and can be more efficient than traditional insulations.
- Applications: Used in high-performance applications where space and weight are critical factors.
Other Specialized Insulations
a. Composite Insulation Systems
- Description: Combining different types of insulation materials to optimize performance.
- Advantages: Enhanced thermal performance, tailored solutions for specific applications.
- Applications: Custom applications requiring specific performance characteristics.
Comparison and Selection
The selection of insulation type depends on various factors, including the specific application, performance requirements, cost considerations, and the physical properties of the stored cryogenic liquid. Here are some key considerations:
- Thermal Performance: Vacuum insulation offers the best thermal performance, particularly when combined with MLI.
- Cost: Foam and granular insulations like polyurethane and perlite are designed to be more cost-effective but may not perform as well as vacuum and MLI.
- Mechanical Strength: Insulations must withstand mechanical stresses during operation and transport.
- Ease of Application: Spray-on foams are more accessible when applied to complex shapes, while pre-formed panels and wraps may be more suitable for standardized shapes.
Safety and Compliance
- Standards and Regulations: Insulation for cryogenic tanks must comply with various standards and regulations, such as those from the American Society of Mechanical Engineers (ASME) and the International Organization for Standardization (ISO).
- Leak Detection: Effective insulation helps in the early detection of leaks by maintaining temperature gradients.
- Fire Safety: Insulating materials must be non-flammable and comply with fire safety standards.
Applications
- Storage Tanks: Used in facilities where cryogenic liquids are stored for long periods.
- Transport Tanks: Used in vehicles and vessels transporting cryogenic liquids over long distances.
- Dewar Flasks: Smaller containers used for laboratory and medical applications.
Advances and Innovations
- Improved Materials: Development of new materials with better insulating properties and environmental resistance.
- Enhanced Manufacturing Techniques: Advanced techniques for applying and bonding insulation materials to cryogenic tanks.
- Integrated Monitoring Systems: Incorporation of sensors and monitoring systems within the insulation to track performance and detect issues.
No comment